BioSafe® Modular Cleanroom Systems
Terra's BioSafe® Modular Cleanroom Wall Systems combine modular design principles with precision-cut prefabricated wall panels. This next-gen design streamlines modular installation and assembly while preserving full design flexibility. Unlike standard modular cleanrooms, BioSafe wall systems are not limited by overhead clearance, size, shape, or pathways within the site. Seamless transitions between ceiling, walls, and floors ensure an airtight, closed system to meet any ISO Class 5–8, GMP A–D, USP, or GLP requirement. The wall systems feature interlocking honeycomb panels lined with a uPVC substrate on both the interior and exterior surfaces. Extruded aluminum edge components enable secure panel interconnection and airtight seams when sealed with silicone, resulting in a flush, contamination-resistant finish.
Hybrid Cleanrooms: Modular Components with Stick-Built Advantages
When compared, Terra's innovative BioSafe Cleanroom Wall Systems emerge as a compelling alternative that combines modular components with stick-built advantages and customization. For companies considering the construction of a cleanroom, there are three primary design options: stick-built (conventional construction), modular construction, and hybrid modular. Each design methodology has distinct benefits; certain applications favor one design over the other, given the specific criteria for industry compliance. Before making a decision, it is important to consider certain design challenges that are inherited by traditional modular and stick-built systems.
BioSafe® Modular Cleanroom Wall Panel Systems
A major selling point of traditional modular cleanrooms is to consolidate the sourcing, fabrication, and delivery of construction materials into a streamlined, simplified process. These systems are quick to return an ROI due to the speed, ease, and repeatability of the construction process. Modular systems offer peace of mind and guaranteed compliance of the final assembly with ISO cleanliness requirements.
BioSafe cleanroom wall panels arrive from the factory with prespecified cutouts for pass-throughs, doors, and windows, which eliminates most on-site modifications that would otherwise require sawing, cutting, or drilling. Modular construction compresses the entire enclosure into flat packed, palletized shipment. With the help of a fork lift, a small team of installers can erect the entire enclosure within a fraction of the time required for conventional cleanroom construction. Meanwhile, traditional framed wall builds might take several contractors weeks or months to complete.
Wall Systems
Wall system features pre-fabricated coving panels to accommodate wall-to-floor and wall-to-ceiling conversions, free of cracks, crevices, gaps.
Ceilings
Ceilings are composed of robust, rugged components capable of handling daily spray-down cycles.
Recessed Channel Bases & Utility Plenums
All panels are installed onto an adjustable height, recessed channel base to ensure a level and flush interface between the wall and the finished floor. Pre-formed corner pieces eliminate the need for surface capping or flashing. Suitable for operating temperature up to 60 degrees Celsius, the pre-fabricated, progressive wall panels are lightweight, cost-effective, and easy to install. The wall panels include a plenum space to house utility and filling lines, providing the user with convenient access to gas, vacuum and water connections, along with duplex outlets, control panels, and phone jacks.
Walkable Hybrid Ceiling System
Terra’s BioSafe® cleanroom ceilings are configurable with standard cutouts for HEPA-filtered fan units, lighting, sprinkler heads, video cameras, fire alarms, power connections, and gas lines. The entire ceiling system is walkable, allowing for easy access to equipment installed above the cleanroom and streamlined maintenance operations, such as HEPA filter change-outs. Importantly, the ceiling panels maintain a flush, seamless surface for easy wipe-down or spray-down to support any cGMP, GLP, ISO 14644-1, and ASTM requirement. The self-supported design suspends using a turnbuckle and hanger assembly, eliminating the need for a T-grid structure.
Seamless uPVC Panels
BioSafe Cleanroom Wall Panels consist of an aluminum honeycomb core encased in a uPVC-laminated steel shell. The 2” thick panels adhere to the ISO 14644-1 standard for ISO Class 5 and cleaner environments. The uPVC laminate finish ensures a fully flush surface that is robust, easy to clean, and resistant to common disinfectants, acids, and corrosives. Seamless transitions between the ceiling, walls, and floors ensure an airtight, closed system to prevent contamination influx.
Explore End to End Services & Solutions
Architecture & Lab Planning
Terra's architectural services offer a dedicated resource when designing large scale facilities with multiple suites, or cross functional spaces that combine cleanrooms, labs, gowning rooms, processing areas, offices, and parallel working spaces.
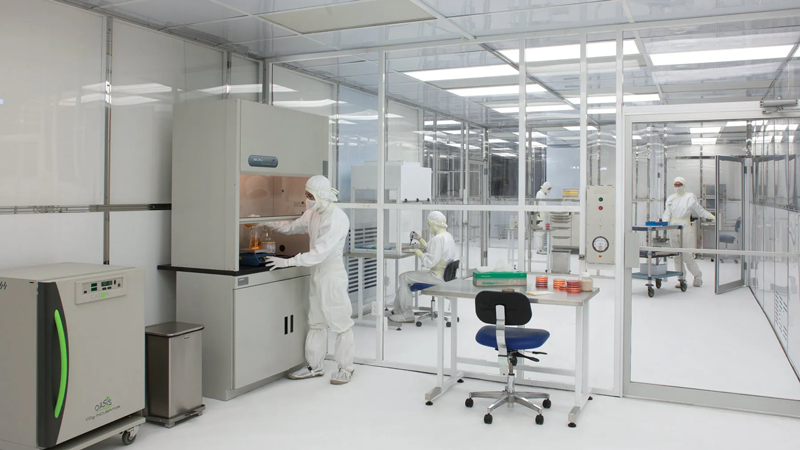
Validation & Commissioning
When a facility design must meet AAALAC, CDC, CGMP, and GLP standards, it is essential to avoid design compromises that hinder the flow of materials, personnel, and products.
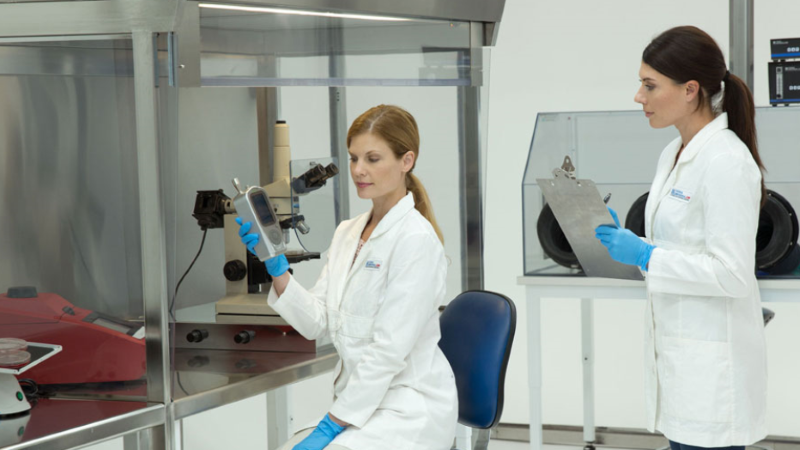
Consulting & Expertise
Our teams comprise decades of expertise in healthcare and pharmacy administration, FDA regulated facilities, issues management, risk management, modeling of healthcare delivery, and safety-quality improvement.
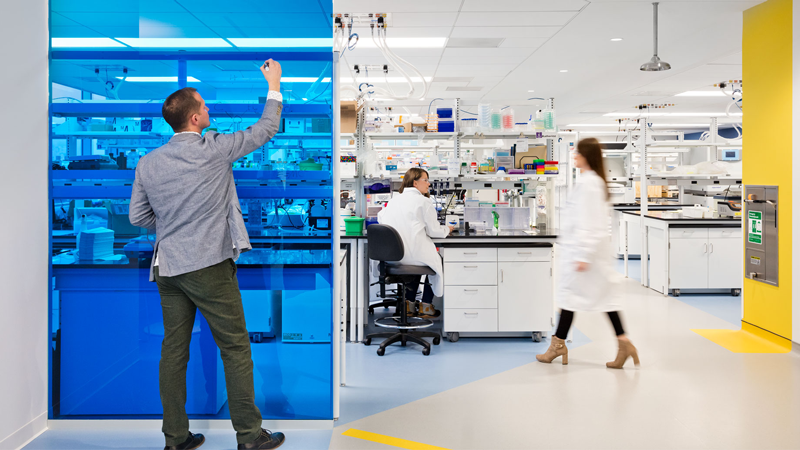
Get a Cleanroom Consultation
Terra offers fully integrated cleanroom engineering design, architecture, construction, and system integration. Rest assured, you'll have a single point of contact for delivering a complete solution.
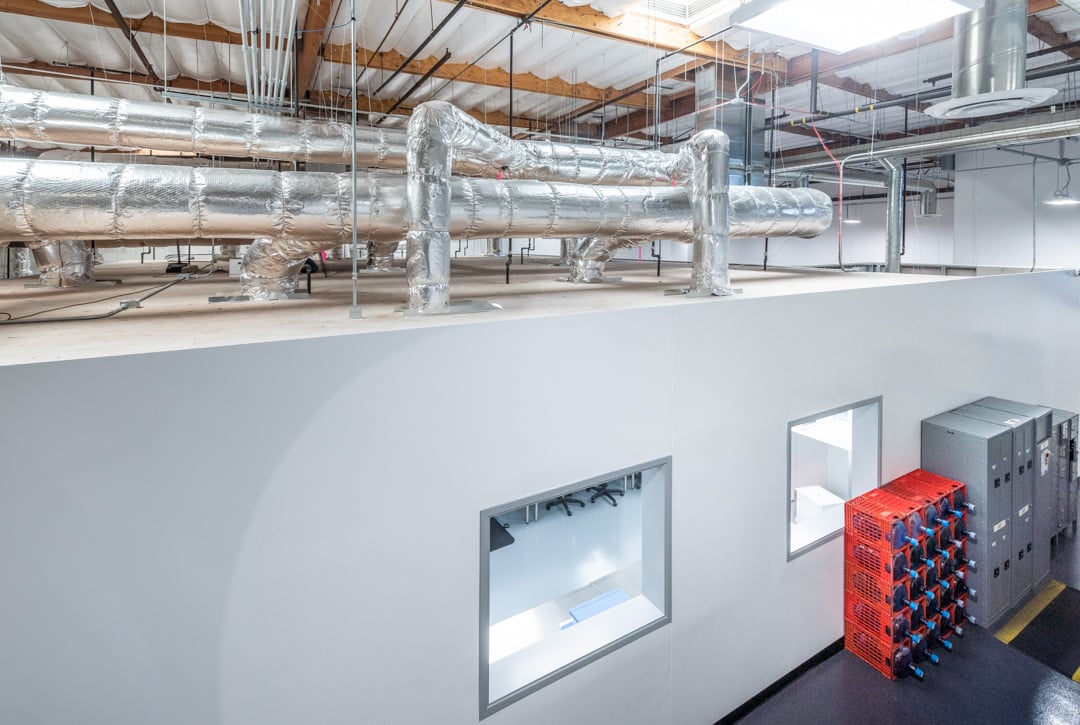
Ask a Terra Cleanroom Specialist
Contact Terra Universal
As a pioneer in the critical environment industry, Terra Universal has developed and manufactured innovative solutions for over 45 years. Combining high-throughput, automated fabrication equipment with a robust, active stock of raw materials, Terra is capable of producing cleanrooms of any design, size, scope, and complexity at industry-leading build times.