Commissioning & Validation
Terra's cleanroom validation and commissioning services include full cGMP documentation packages, equipment qualification, re-qualifications, and operational services to support continued GMP/FDA compliance. All of our validation services are thoroughly documented and undergo a quality assurance review before being released to the customer.
Commissioning
Terra's Commissioning Plans include ISO 4 — ISO 8 cleanroom commissioning services, as well as Biosafety Level 1–4 laboratories. The commissioning process begins at the conceptual phase of a project and extends through design and construction, continuing for at least one year post-construction to ensure thorough validation of building systems.
Testing & Validation
Terra's cleanroom validation extends beyond individual equipment to encompass the entire operational environment. This holistic assessment addresses all aspects of cleanroom functionality, including gowning procedures, disinfection protocols, planned maintenance, risk mitigation, document traceability, and quality assurance and control measures.
Qualification
Terra's IQ/OQ protocol assessments extend beyond individual equipment to encompass the entire operational environment. This assessment addresses all aspects of cleanroom functionality, including gowning procedures, disinfection protocols, planned maintenance, risk mitigation, document traceability, and quality assurance and control measures.
Cleanroom Commissioning Services
Executed as a global exercise, cleanroom validation is a method of establishing documented evidence, with a high degree of assurance, that the manufacturing process will consistently yield a product of predetermined quality. If a manufacturer fails to execute a comprehensive equipment qualification, they may experience rising product failure rates, production inefficiencies, employee miscommunication due to incomplete standard operating procedures and, potentially, a loss of market share. This risk can be mitigated by performing an IQ/OQ/PQ on your cleanroom and equipment.
Cleanroom Commissioning is a systematic process of ensuring that a building performs by the design intent, contract documents, and the facility's operational needs. (Department of Energy). Due to the sophistication of cleanroom designs and the complexity of their associated systems, commissioning is necessary for GMP builds, but not automatically included as part of the typical cleanroom design and contracting process.
Building Commissioning Services
Building commissioning ensures that all systems within a building, including mechanical (HVAC and refrigeration), electrical, lighting, safety controls, plumbing, and specialized equipment operate according to specifications. This process verifies that the chosen products and systems meet the manufacturer's claims and are suitable for the intended project.
Commissioning is crucial not only before and during the initial occupancy, but also throughout the life of the building process to accommodate use changes and system wear. Continuous commissioning or periodic recommissioning is necessary to maintain operation in line with the original design intent and construction documents. This practice involves checking and optimizing systems, such as ensuring air flow in ventilation systems is unimpeded by clean filters for efficiency, comfort, and health.
The commissioning of a cleanroom unfolds through several distinct stages, each critical to certifying its operational efficacy and environmental regulation from inception to active use. Effective commissioning strategies typically render the following optimizations and improvements during the build process:
- Energy savings and persistence of savings
- Improved thermal comfort with proper environmental control
- Improved indoor air quality
- Simplified operation and maintenance documentation
- Improved system function that eases building turnover from contractor to owner
- Consistent system function when the building turns over from one operator to another
Terra's Commissioning Plans
Terra's Commissioning Plans include ISO 4 — ISO 8 cleanroom commissioning services, as well as Biosafety Level 1–4 laboratories. The commissioning process begins at the conceptual phase of a project and extends through design and construction, continuing for at least one year post-construction to ensure thorough validation of building systems.
Starting early in the design phase to integrate commissioning requirements into the project, it's important to outline special requirements in bidding documents and select contractors familiar with the commissioning process.
- Coordinating both static and dynamic testing to confirm system performance.
- Concluding with comprehensive staff training on system operations and ongoing warranty monitoring.
- Evaluation of building envelope and interior finish materials
- Laboratory-specific process checks to ensure a holistic approach to building performance and sustainability.
Operational Services & Support
Terra provides an end-to-end service model to its clients, encompassing both up-front solutions and recurring services that are tailored for longer-term risk management and procedural compliance.
Up-front Services
- GMP Roadmaps: Create a strategic plan for achieving and sustaining GMP compliance.
- Risk Mitigation Strategies: Implement robust plans to minimize risks associated with operations.
- Standard Operating Procedures (SOPs): Develop detailed instructions for quality and consistency of core processes
Ongoing Support
- SOP Updates: Maintain compliance by adapting SOPs to new regulations and operational protocols.
- Recommissioning: Ensure equipment and systems are updated and calibrated to current needs.
- Shutdown Support: Facilitate planned maintenance activities to optimize system longevity and reliability
ISO Cleanroom Validation Services
Provide Terra with your desired ISO rating, and we will tailor the product to meet your rating and certify it with the part numbers appended to your invoice. Certificates of compliance formatted as a PDF file for easy sharing with colleagues or auditors and stored in Terra's digital archives for quick retrieval.
Cleanroom Testing & Certification Services
Certification of a cleanroom or processing equipment can be as simple as performing a smoke study or a HEPA filter leak test. Certification testing protocols often don’t account for variables that may affect the final environment. An IQ/OQ protocol accounts for all known variables, performs a deeper verification of the equipment, and integrates all documents into a single, comprehensive file.
Sensor Calibration: All sensors and gauges must be calibrated and documented with a date-stamped calibration sticker. The validation process requires proof that each system has been tested and will provide the same output of results during regular operation.
Viable Surface and Air Testing: A proper IQ/OQ protocol includes a drafted and tested cleaning procedure. To ensure the cleaning procedure was effective in removing all viable microbes, a viable sampling test is performed on the same day as the IQ/OQ validation.
Airflow Visualization Study: A smoke study is required to show the air flow pattern inside a process enclosure, such as a glove box or cleanroom. Air flow laminarity, uniformity, turbulence, and air velocity are evaluated during the study.
Filter Leak Testing: A test to ensure the HEPA filters are not damaged, the filter media is not saturated and the filter effectively captures particulates per stated specifications.
IQ/OQ/PQ Services
Once you have purchased the IQ/OQ package, a Terra Universal validation specialist will get in contact and set up a phone call. During the initial phone call, all customer requirements will be discussed and validation questions answered. The protocol is then drafted and sent to the customer for approval. Once approved, Terra's validation specialists will arrive on site (if needed) to execute the validation protocol. Once complete, a full report along with all data is sent for client approval.
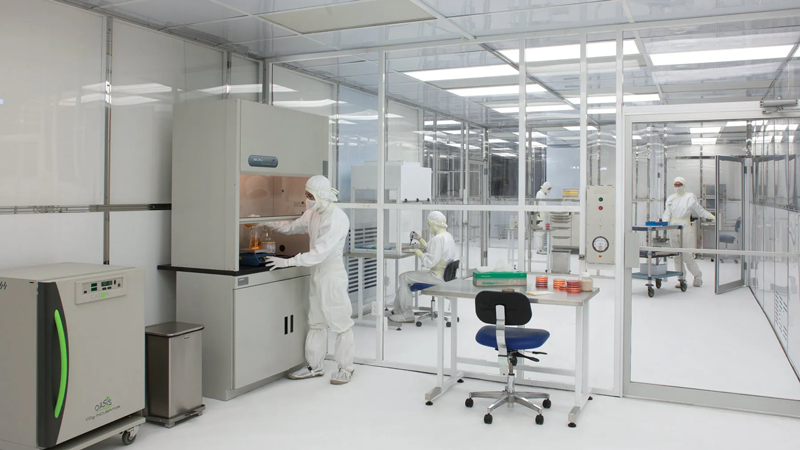
Equipment Qualification & Validation
Equipment Qualification includes three stages: Installation Qualification (IQ), Operational Qualification (OQ), and Performance Qualification (PQ). IQ confirms that equipment is installed following manufacturer's specifications, OQ verifies that it operates as intended under various conditions, and PQ ensures consistent performance over time. This comprehensive "IQ/OQ/PQ" framework is particularly vital for specialized equipment like glove boxes, establishing a robust foundation for quality and compliance.
Terra's rigorous equipment validation packages encompass:
- Installation
- Qualification (IQ)
- Operational Qualification (OQ)
- Performance Qualification (PQ),
- Construction Qualification (CQ),
- Factory Acceptance Testing (FAT),
- Site Acceptance Testing (SAT),
- User Requirement Specification (URS),
- Statement of Work (SOW)
- Feasibility Studies
These comprehensive validation steps ensure that equipment not only meets stringent industry standards but also aligns with client-specific requirements. Contact a Terra Universal product specialist allows for direct consultation with the validation engineering team to tailor the validation process to the project's unique specifications.
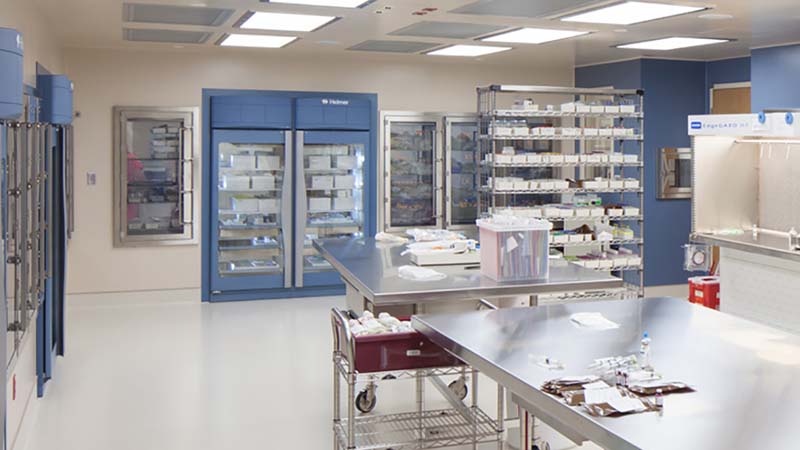
Application Consulting
Terra offers end-to-end solutions to establish and maintain validation programs that are both reliable and compliant with regulatory standards. By focusing on lowering operating costs and compliance, efforts are harmonized to ensure that every phase of product development, from conception to market launch, meets the necessary quality and regulatory requirements. This approach facilitates the smooth transition of products through development, validation, and commercialization stages, enabling clients to achieve their market objectives with efficiency.
Extended Services
Terra's cleanroom testing and certification services are designed to ensure the optimal performance of the cleanroom, as well as its associated filtration systems, clean air benches, laminar flow hoods, and other cleanliness reliant systems. Validation protocols ensure that equipment not only meets stringent industry standards as well as any application-specific requirements.
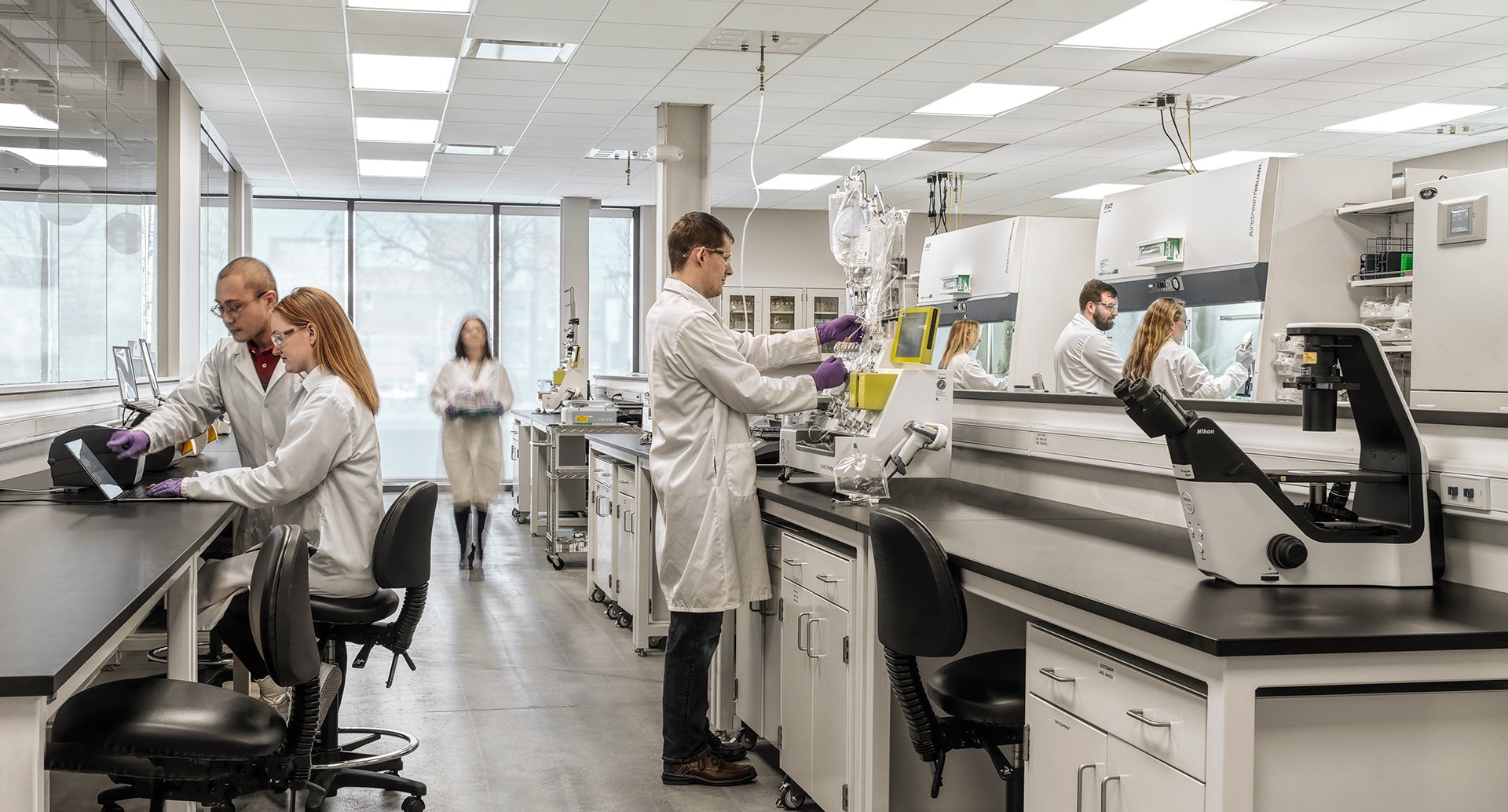
Get a Cleanroom Consultation
Terra offers fully integrated cleanroom engineering design, architecture, construction, and system integration. Rest assured, you'll have a single point of contact for delivering a complete solution.
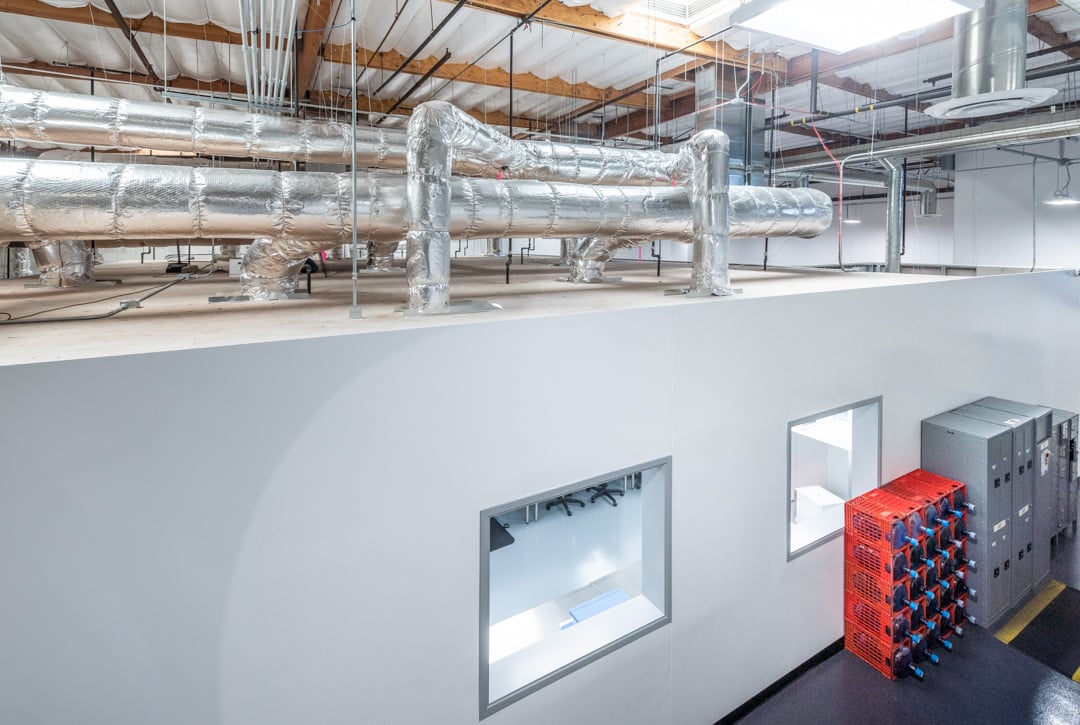
Ask a Terra Cleanroom Specialist
Contact Terra Universal
Combining high-throughput, automated fabrication equipment with a robust, active stock of raw materials, Terra is capable of producing cleanrooms of any design, size, scope, and complexity at industry-leading build times.
Global Vendor Network
Terra's network offers over 20 global sales regions and 80 major suppliers with a wide range of global shipping options. Get door-to-door international delivery for brands such as Labconco, Thermo Fisher, Metro, Eagle, Biofit, and Germfree
Get a Cleanroom Consultation
Terra offers fully integrated cleanroom engineering design, architecture, construction, and system integration. Rest assured, you'll have a single point of contact for delivering a complete solution.
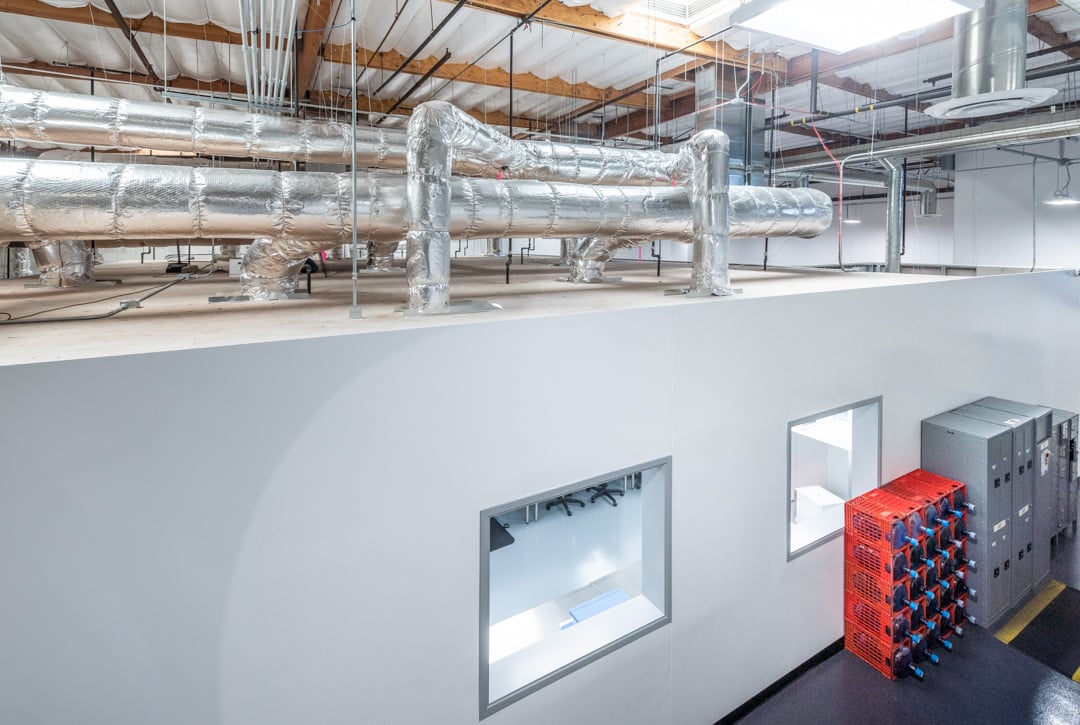
Ask a Terra Cleanroom Specialist
Cleanroom Design & Engineering
Building commissioning is an essential process to ensure that all systems within a building, including mechanical (HVAC and refrigeration), electrical, lighting, life safety, plumbing, and specialized equipment like laboratory apparatus, perform optimally and according to specifications. This process verifies that the chosen products and systems meet the manufacturer's claims and are suitable for the intended project.
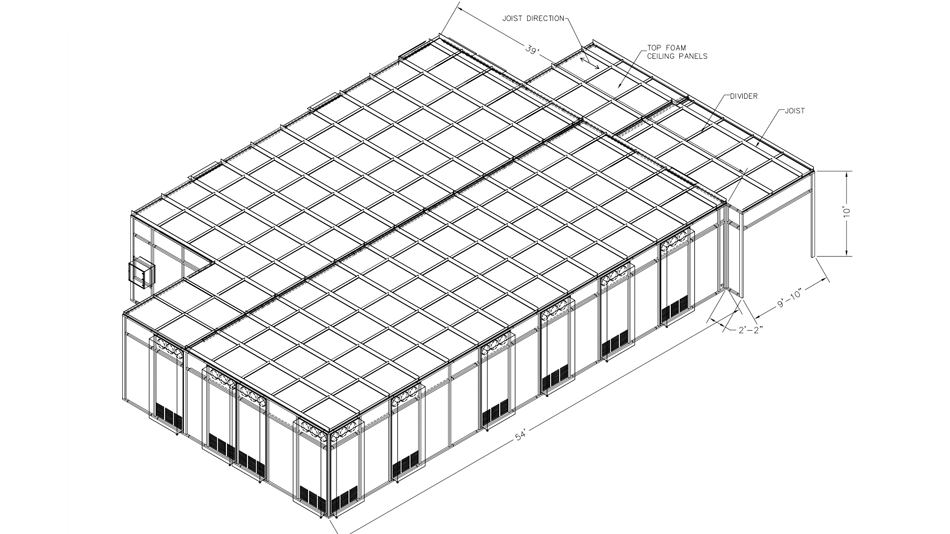